The Challenge
The Acuity Brands Lighting Midwest Distribution Center (MWDC) and operations facility in Des Plaines, IL needed a relight. While the investment would provide an additional layer of energy savings, the project also presented an opportunity for the facility team to leverage their lighting upgrades to optimize how they were using their space. Incorporating indoor positioning technology from Atrius to their intelligent lighting systems would help MWDC justify the expense of the relighting project.
The Solution
Collaborating with Acuity Brands Lighting and Atrius teams, the MWDC facility leaders customized a solution with a three-and-a-half- year payback that justified the investment to install lighting equipped with location services.
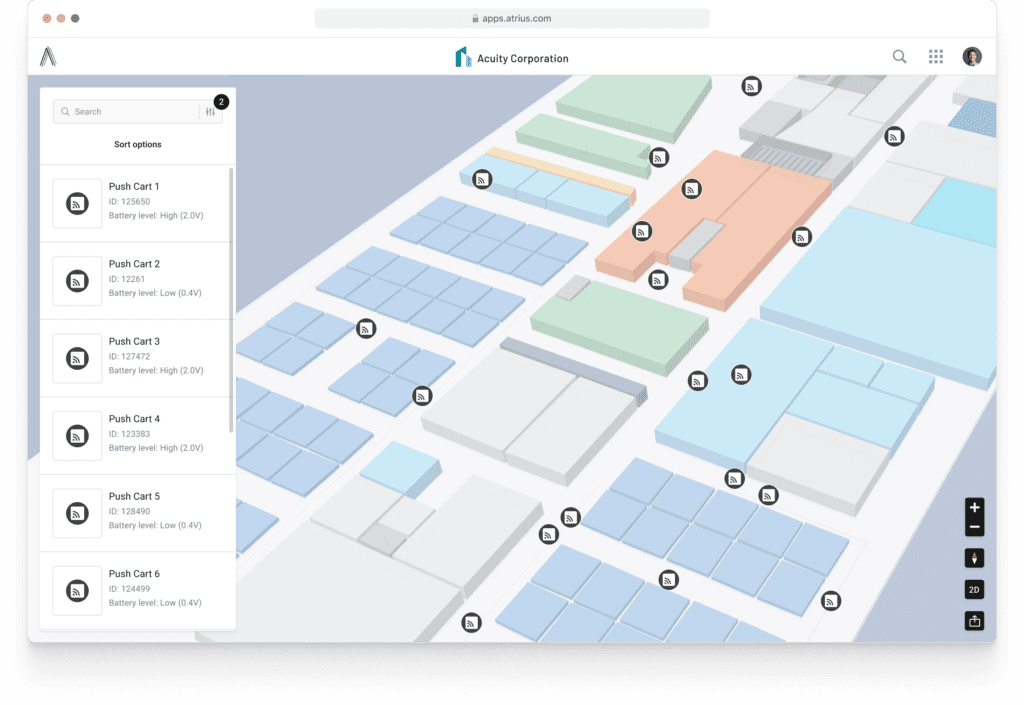
Re-lighting the 480,000 square foot facility included qty 864 IBG high bay LED luminaires equipped with Light Air controls from Acuity Brands. The team reduced the number of devices, required wiring, and installation tasks necessary to deliver location services by utilizing lighting and wireless controls as the common-use platform for the newly implemented RTLS infrastructure.
“Data from Atrius utilization charts and heat maps revealed an opportunity to load-level fork-lift equipment across an additional shift, enabling us to reduce the number of lifts in the building.”
During the re-lighting project, leadership realized they could increase ROI with the cloud-based Atrius Locator item tracking feature. They attached small, battery-operated tags to forklifts and frequently moved palletized product.
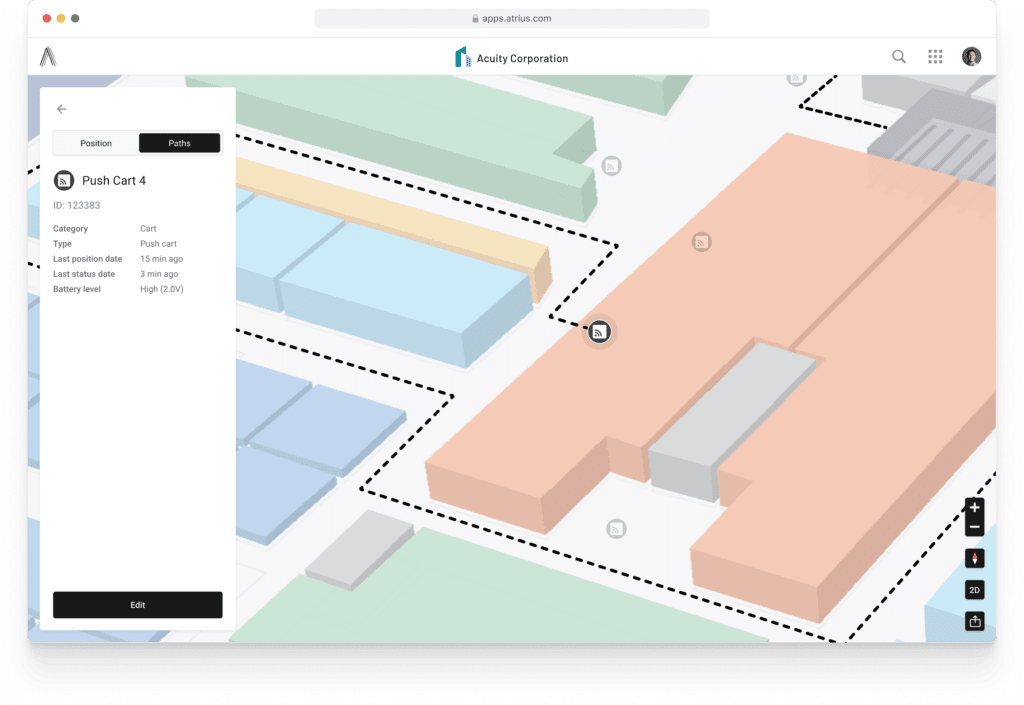
Suddenly, facility team members could understand how high-value items were moving within their space through maps and dashboards displaying standardized turnkey analytics. This enhanced functionality further justified the value of investing in real-time location services (RTLS), but also revealed surprising usage insights.
The newly acquired tracking data confirmed only 75% of the forklift fleet was utilized simultaneously during a given work shift. Sidelining the under-utilized trucks for a set validation period proved management could reduce fleet expenses without jeopardizing productivity. They eliminated the leased trucks and adjusted maintenance schedules for the owned trucks.
“Atrius solutions helped us save $1MM in operating costs and accelerated project payback by 2.5 years.”
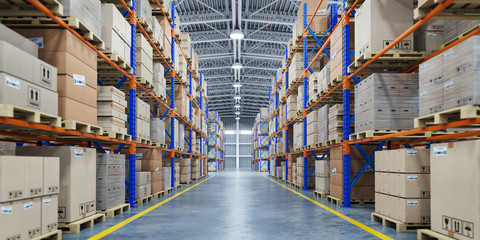
The Results
By leveraging the value of Atrius location services, project managers accelerated the $425K MWDC relight investment from a three-and-a-half-year payback to only one year. In total, the facility saved a combined $1MM in electrical costs and forklift lease and maintenance expenses.
The turnkey Atrius solution enabled a quantifiable ROI with immediate and recognizable impact on the facility. Acuity Brands is optimizing the success of the MWDC relight and RTLS implementation, projecting Southeast and West Coast distribution centers will be online by mid-2022.
Download a Copy of the Case Study
Interested in a hard copy of this case study? Take a look at the PDF version here.