Warehouse energy consumption costs weigh heavily on operating budgets. Given their immense square footage, extensive operating hours, and need for powering heavy equipment, warehouses have high energy demands.
Yet, there’s no way to know which strategies for energy reduction to apply without collecting warehouse energy data. An energy management system is key to tracing and optimizing energy use in warehouses. This intel can lead to creative energy efficiency strategies.
Key facts about U.S. warehouse energy consumption:
- 17% of commercial buildings in the U.S. are warehouse and storage buildings.
- 8% of fuel costs spent in commercial buildings are from warehouse and storage buildings.
- Warehouse space heating accounts for approximately 39% of end-use energy consumption.
- Lighting makes up 15% of total energy consumption in warehouses.
Source: U.S. Energy Information Administration 2018 Commercial Buildings Energy Consumption Survey
Motivations for warehouses to become energy-efficient
Aside from the obvious cost-saving benefits, warehouses are among many commercial buildings subject to energy benchmarking and performance standards, which are expanding around the U.S. These standards require the owners of commercial buildings to implement steps to measure and/or reduce energy to achieve specific energy efficiency targets.
States adopting these regulations do so to meet their own climate goals since commercial buildings account for 40% of carbon emissions in the U.S. The long-term community-wide benefits of lowering energy consumption include climate resilience and healthier air quality in local environments.
Pinpointing the main sources of warehouse energy use
The energy management process starts with measurement to identify the main sources that contribute to the energy consumption footprint of a warehouse. Atrius Energy simplifies measurement by automating data uploads at the meter and sub-meter levels in real-time. Based on these measurements, energy managers can start to untangle the web of energy sources contributing to the high energy bills they receive from utilities.
These sources will vary based on a warehouse’s main function and seasonal temperature requirements. Some warehouses are refrigerated spaces where food is processed. Other warehouses require heating in winter and cooling in summer. Due to their size, their heating equipment may differ from standard central heating systems.
With Atrius Energy’s dashboards, energy managers can also examine the peaks and valleys of energy use by source across daily, weekly, monthly, and annual time periods.
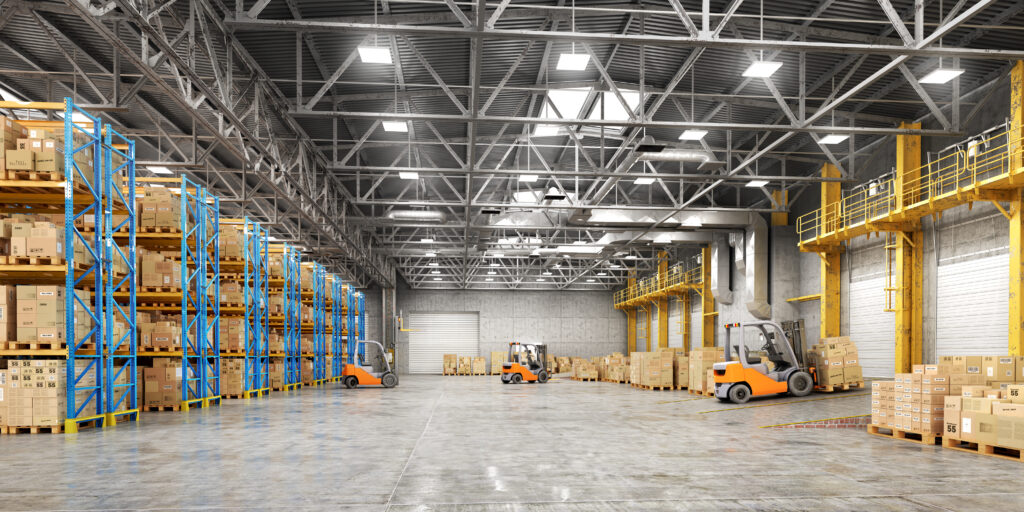
Innovative energy efficiency strategies
- LED Lighting: LED lighting is a well-known alternative to metal halide lights, the conventional lighting used in warehouses. Unlike metal halide bulbs, which take a long time to light up, LED bulbs illuminate instantly, lowering wasted energy. LED lights can also switch on and off with motion sensors, so no energy is wasted in non-active parts of a warehouse space.
- Lighting Placement: The Acuity Brands Lighting Midwest Distribution Center (MWDC) and operations facility in Des Plaines, IL, chose to upgrade its lighting for energy efficiency. Atrius Energy helped the warehouse analyze its operational use of the space to place lighting in a newly rewired arrangement strategically. This approach lowered the lighting units required to light the space and the cost of replacement. The same approach can be used to analyze the functional use of lighting in each area of a warehouse such as loading docks, parking lots, and storage areas.
- Offsetting Retrofit Costs: Optimizing warehouse spaces for cost reduction can come from other operational improvements, too. MWDC analyzed its forklift fleet use and routes during operations to further lower costs by attaching sensors to its equipment that could communicate data to the Atrius Energy dashboard. Using this technique, MWDC discovered that it used only 75% of the forklift fleet, which enabled it to reduce its fleet size and identify additional savings for funding its lighting project.
- Building Air Flow: Warehouses and distribution centers are hubs of activity where freight is transported, and shipments enter and exit the warehouse through large doors where air from outside can easily enter the building. Maintaining internal air temperatures with heating and cooling equipment can be a challenge. Strategies to reduce air leaks include weather stripping, cushioning doors, insulation, and seals to prevent leaks at loading bays.
- HVAC Equipment: In the U.S., warehouse heating equipment includes individual space heaters (22%), packaged heating units (20%), and furnaces (19%). Mapping where leaks occur based on the building structure can help identify the most effective solutions for equipment-based temperature and energy cost control. Examples include floor heating, ceiling fans, tube heating, and more. Using an energy management platform to schedule routine maintenance for HVAC equipment helps ensure heating costs don’t result from poorly functioning equipment.
- Installing Roof-top Solar Energy: Generating energy for use within warehouse operations is another approach to minimizing energy costs long term, though it does have a significant upfront cost. Warehouses feature large rooftop areas that can often accommodate a substantial array of solar panels. The U.S. Department of Energy (DOE) Better Building Challenge demonstrates how successful partnerships through green leasing can support warehouse tenants in enhancing renewable energy installation opportunities. Installing photovoltaic (PV) panels is a highly visible and inspiring way to engage both tenants and employees in the importance of both energy cost savings and clean energy.
- Energy Demand Shifting: Small adjustments through system-wide equipment interactions, maintenance, and optimization can shave off significant costs over time. Understanding how energy loads compound at peak usage times can enable strategic decision-making related to equipment use.
Identifying, tracking, and monitoring the full range of strategies available to warehouse energy managers requires a centralized data management hub for energy-related activities. Atrius Energy captures the insights necessary to weigh the costs and benefits of upgrades.
Taking the first step
Warehouses are no strangers to operational efficiency, which is key for their distribution, shipping, and logistics processes. Applying the same logic to energy is the next step that warehouses can take. Whether it’s to address increasing pressure from rising energy costs linked to inflation or new regional building standards, now is the right time for warehouses to measure and understand their energy consumption. The first step to measuring energy consumption with precision is setting up an energy management system. Atrius Energy is an easy-to-use system for implementing a wide range of energy efficiency strategies.