This article was originally published by BUILDINGS.
Season after season of searing heat and rolling brownouts are leading to higher than ever energy costs. The National Oceanic and Atmospheric Administration recently reported that the average July temperature in the contiguous U.S. was the third warmest July in its 128 years of record-keeping. Facility managers who have detailed data around energy allocation and how people are using their spaces can respond faster to environmental stressors and enable safer, more efficient buildings.
Hotter summer days means more air conditioning is required to keep people comfortable and equipment running smoothly. But it’s expensive—HVAC systems account for more than 40% of a commercial building’s total energy use, a level of consumption called one of the most critical issues of our time by the International Energy Agency.
Solutions that compile data about every aspect of a building’s current conditions—the real-time energy draw, temperatures, air quality and how the space is being used—can autonomously take effective actions. These technological solutions can work for both new and existing commercial buildings and can help operators maintain energy-efficient buildings. Connected hardware that senses and acts on changing conditions are more efficient compared to laborious manual recording and hands-on adjustments.
It’s important to take the necessary actions that adopt supportive technology that can provide facility managers the information needed to make informed decisions.
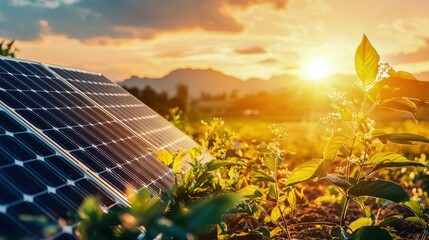
Compiling Data for Intelligent Action
The first step in preparing for extreme summer conditions is having a deep understanding of past and current energy patterns. Predictive modeling technology that analyzes vast amounts of historical and current data can result in a 20-30% energy reduction.
A thorough energy analysis will establish baselines, identify indoor temperature patterns and trends for future scenarios, and can aggregate information from local utility providers and weather forecasting. These data sets give operators the information they need in planning switchovers to generators or alternate energy sources, using energy most optimally. The Environmental Protection Agency estimates that on average 30% of energy used in existing and new commercial buildings is wasted, proving there are vast opportunities to conserve and manage energy.
Opportunities to Lower Energy Use Without Sacrificing Comfort
One of the leading considerations for deciding prime room conditions is occupant comfort. Temperature and air quality have a significant impact on productivity, morale and job performance. A study by the U.S. Department of Energy examined how indoor air temperature impacts office workers, determining that 71 to 72 degrees F. was the ideal range for peak performance.
Cranking up the air conditioning on a hot day might seem the easiest course to cool people off, but it’s not necessarily the right decision for every environment. Building operators need to take into consideration the office layout, occupancy levels, activities underway, humidity and other air quality conditions.
When balancing peak loads against extreme temperatures, operators can explore additional actions to enhance comfort. For example, knowing that a hot day is expected, changing HVAC operations to cool the building earlier in the day before peak loads can reduce demand charges. Installing ceiling fans that are activated in advance of sweltering afternoons can keep the building more comfortable. Dimming lights in areas where few people are expected lowers costs too. Smart sunshades that detect sunlight can be set in motion through automation or occupant control.
A connected system of hardware sensors aligned with continuous learning from AI will “know” when to dim lights, activate shades or fans or adjust humidity levels based on historical trends, predetermined parameters, and the number of people in each area. An example of responsive technology is a smart thermostat controller that’s integrated with automation tools that acts upon changing conditions without the need for manual intervention. Autonomous tools that work seamlessly together can pinpoint evolving situations and respond accordingly.
Preventing Problems Through Predictive Modeling
Predictive modeling tools detect changes in patterns and can identify problems before they arise, warding off expensive breakdowns in equipment and proactively addressing equipment life cycles. Because extended heat conditions affect the quality and efficiency of HVAC systems, they might require more preventive maintenance throughout the summer. Manual inspections and reactive repairs are more expensive. A continuous monitoring and data analysis system can identify problems before they become expensive emergencies.
Tracking everything from filters to ductwork to equipment life cycles is expensive and laborious to do by manual methods. But simply setting the routine maintenance and cleaning of this equipment on schedules without regard to usage and how the equipment is actually functioning can also be a waste of resources.
Over-use of equipment can also add more wear, tear and expense. For example, ventilation systems remove carbon dioxide and draw fresh air to spaces. But depending upon occupancy levels, not every area of a building requires that level of constant ventilation. Demand-control carbon dioxide sensors that monitor real-time air quality conditions replace air as needed, not based on peak occupancy.
Predictive modeling technology collects data on past performance and compares it to current operating activity. This gives operators a better view of how equipment is working and when it requires upgrades. When office equipment is not being used, shutting it down completely can create significant financial and energy savings.
Reducing energy consumption in the face of increased demand is a challenge but can be managed with data analysis, predictive modeling technologies and automation. The key is integrating simple to use but smart building automation tools that work with both existing buildings and new construction. As commercial building operators brace for another searing summer, a focus on having real-time data, continuous monitoring and analysis systems in place will help them keep buildings safer, greener and sustainable.